ESPRIT SolidMill® is a full-spectrum suite of milling cycles for facing, roughing, contouring and finishing, and hole making. With ESPRIT’s Modeless Programming™, these cycles are universally available on any class of CNC machine: vertical, horizontal, and gantry mills, millturn, and lathes — including Swiss-type. With SolidMill cycles, quickly generate efficient milling toolpaths while keeping extensive control over the movements of the cutting tool, supporting unique requirements of individual parts. Automatic calculation of the stock allows the system to generate efficient toolpaths while avoiding tool breakage and collisions. Machine-optimized G-code uses the advanced functions of the CNC, such as helical and polar interpolation, high-speed and high-precision options, and the machine’s built-in canned cycles.
In short, SolidMill:
-
Is a full-spectrum suite of milling cycles universally available for any class of CNC machine
-
Quickly generates toolpath with extensive control to support the unique requirements of each part
-
Produces edit-free, machine-optimized G-code
Model-Driven Machining
Starting from the CAD model, ESPRIT analyzes the part geometry to identify the machinable features. The machining cycles use the feature properties such as depth, draft, and hole style to minimize manual input, speeding the programming process and reducing the risk of error. Each feature is automatically associated with a workplane that drives a 4th or 5th axis to orient the workpiece. If the CAD model is updated, the associated toolpath is automatically updated to reflect the changes to the geometry.
​
-
Knowledge of the part is used to simplify programming
-
Speeding the programming process and reducing chances for errors
-
Automatic workplanes for 3+2, 4th or 5th axis, part orientation
-
Automatic association updates to the toolpath, reflecting changes to the geometry
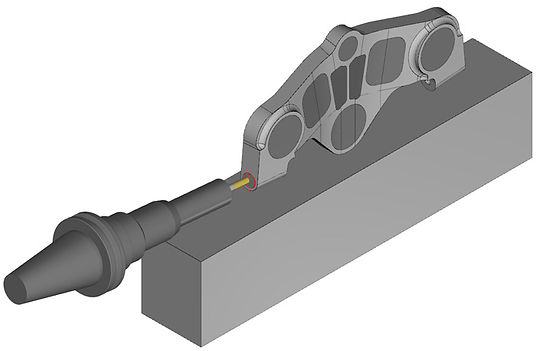
​
-
3+1, 3+2, and rotary machining options
-
Cycles provide extensive control over the toolpath
-
High-speed machining built into each machining cycle:
-
Constant cutter loads to minimize tool deflection
-
Slotting strategies for narrow channels
-
Bottom-up roughing to minimize cutting time
-
Spiral-style cutting with constant overlaps
-
Sharp corner smoothing
-
Ramp and helical entry into material
-
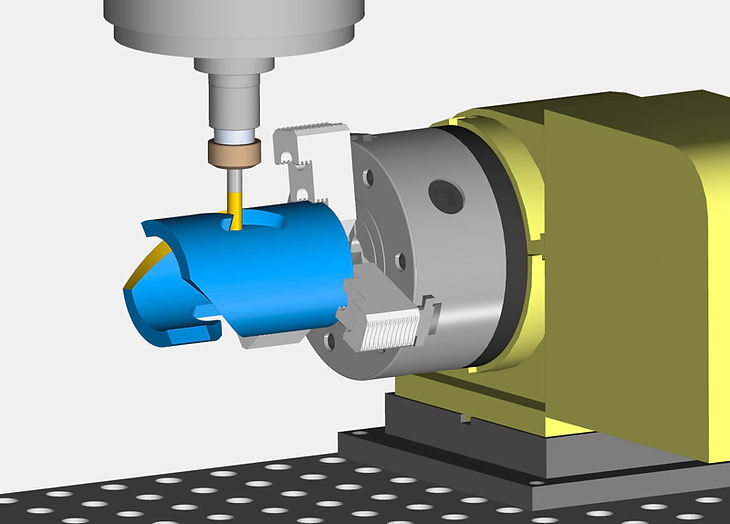

Holemaking
Use the holemaking cycles to produce a wide variety of hole styles including blind, through, interrupted, deep, threaded, countersink, and counterbore. With the option of using a spinning tool, a spinning workpiece, or both, ESPRIT’s suite of holemaking cycles are suitable for use on both a mill and a lathe. Working from a hole feature containing a set of properties that define the hole style and its geometric shape, ESPRIT’s holemaking cycles quickly produce toolpaths optimized for a minimal cycle time for any number of holes.
​
-
Quickly produce toolpaths optimized for minimal cycle time
-
Machine a wide variety of hole styles: blind, through, interrupted, deep, threaded, countersink, counterbore, and more
-
Suitable for use on both a mill and a lathe
-
Using a spinning tool, a spinning workpiece, or both
Programming Automation
Adaptive Machining Cycles

Starting with the digital machine, templates are used to define the common settings for a given class of parts. The component libraries define the workholding and fixturing, making a quick job of the setup process. Tooling libraries provide an easy method to tool up the machine for the given job. Using the shop’s established set of processes and methods, setting the cutting condition for each cycle is quickly done and processes are consistent across jobs, providing repeatable results.
​
-
Captures and reuses machining methods for automation and consistency
-
Templates for common setting for a given class of parts
-
Libraries of workholding and tooling for quick machine setups
-
Repeatable results using a shop’s established best practices
ESPRIT’s SolidMill machining cycles adapt to take full advantage of the machine’s capability, including offering rotary machining with polar interpolation. This can be applied to any cycle when the rotary axis is parallel to the tool axis, resulting in optimized tool travel. These cycles provide extensive control over the toolpath, including a broad choice of approach, entry, exit, and retract strategies to assure the tool is not shocked as it enters or leaves the material. Feedrates, clearances, offsets, and many more technical parameters are managed throughout the cutting process to produce optimal results. All SolidMill cycles may be used with one, two, or three rotary axes to orient the part prior to machining. ESPRIT manages this process automatically based upon the machine’s axes and the workplanes used during programming.

Facing & Roughing
ESPRIT has a collection of cutting cycles for rough machining; the most powerful is the pocketing cycle. Pocketing quickly removes large volumes of material for pockets and cavities that may include islands, bosses, and subpockets. This flexible cycle creates a toolpath that progressively removes the material inside the boundaries at incremental depths optimized for the remaining stock as the cycle progresses. The cycle handles open or closed shapes that may be blind or through. Within a single pocketing operation, the cycle can create roughing passes, wall finishing passes, floor finishing passes, or any combination of the three.​
-
A collection of cutting cycles for rough machining; the most powerful is the pocketing cycle
-
Quickly removes large volumes of material for pockets and cavities that may include islands, bosses, and subpockets
-
A single cycle can create roughing passes, wall finishing passes, floor finishing passes, or any combination of the three

Contouring & Finishing
SolidMill contouring is an extremely flexible cutting cycle suitable for a wide variety of machining needs for roughing and finishing of open and closed shapes. Contouring operations are commonly used to remove material along vertical or tapered walls and to cut chamfers along the edges of a part. A single operation may perform roughing and finishing with multiple passes for stepovers and incremental depths. Automatic trimming of the toolpath to the remaining stock further minimizes cycle times.
​
-
Flexible cutting cycle suitable for a wide variety of machining needs
-
Roughing or finishing of open or closed shapes
-
Minimizing cycle time by automatically trimming the toolpath to the remaining stock
Optimized for Remaining Stock
ESPRIT performs real-time management of the remaining stock within and between operations as well as across setups, resulting in shorter cycle times and assuring collision-free machining. The remaining stock is available for visualization at any step in the process plan, and simulation may be started at any point in the program using this same stock. Dynamically monitoring the stock during the cut eliminates air cutting and allows remachining to remove remaining material left over from larger roughing cutters.
​
-
In-process stock models eliminate air cuts and minimize repositioning for shorter cycle times
-
Remaining stock may be visualized at any time in the process plan
-
Simulation can start any time using the same stock


ProfitMilling
This high-speed machining cycle is designed for roughing to significantly reduce cycle times and increase tool life. Its patented technology automatically manages chip loads and lateral cutting forces, while also maintaining the cutter engagement angle and machine axes acceleration within ideal ranges. With ProfitMilling, the machine can take deeper cuts at increased feedrates which are also automatically tuned throughout the toolpath for optimal results. Compared to traditional machining, ProfitMilling delivers:
-
75% reduction of cycle time
-
500% increase in tool life
SolidMill Cycles
-
Facing: Removes material on a flat surface with linear cutting passes
-
ProfitMilling: A high-speed machining cycle for roughing that significantly reduces cycle times and increases tool life
-
Pocketing: Offers any combination of rough and finish cycles for pockets, walls, and floors
-
Contouring: A universal machining cycle for rough and finish machining profiles, boundaries, chamfers, or part features
-
Drilling: Holemaking cycles for blind, through, deep, threaded, countersunk, and counterbored holes with the option of using a spinning tool, a spinning workpiece, or both
-
Spiraling: Creates a milling operation in the shape of a spiral on the inside or outside of cylindrical shapes
-
Threading: Internal or external thread milling
-
Wireframe Milling: Creates 3D milling operations from two-dimensional profiles
-
Manual Milling: Creates a milling operation along manually selected geometric elements or locations
-
Engraving: Creates a milling operation to engrave text with multiple options to control the font, size, and orientation of the text. Choose from three strategies: centerline contouring, V carving, or concentric pocketing
